Healthy Cooling Systems
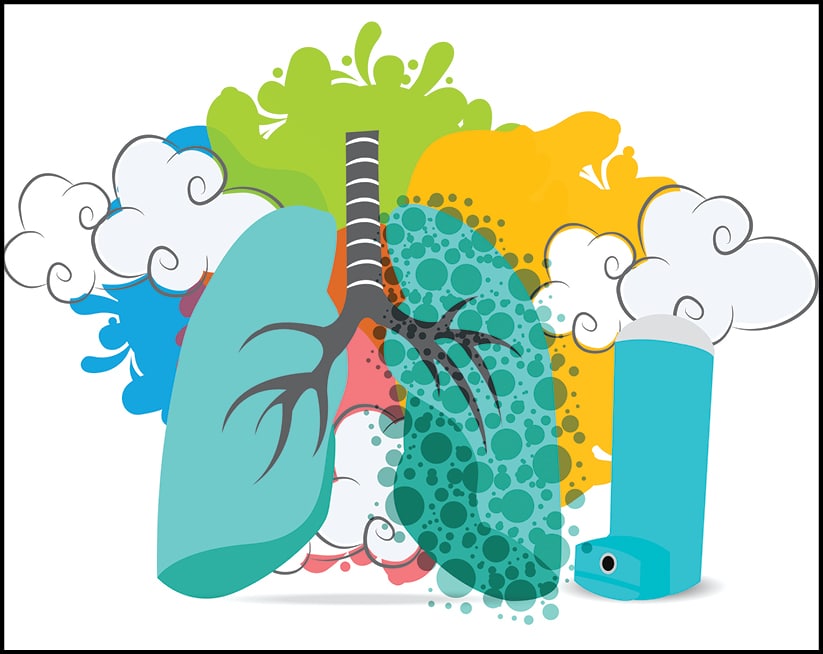
I once compared conditions in 300 randomly selected homes I inspected as a home inspector to 600 “sick homes” I inspected as an indoor-air-quality professional; these were houses where occupants were suffering from asthma and/or allergy symptoms. About 19% of the control houses had central A/C, but 37% of the “sick homes” had central A/C—thus the sick homes were almost twice as likely to have central air conditioning.
The installation of air conditioning is the cause of sick-building symptoms in communities around the world. In my work I often find A/C coils and drip pans colonized with bacteria, yeast, and/or mold. A small portion of these biological materials becomes airborne every time the system operates. The odor (strongest at start-up) associated with contaminated systems is the stink associated with the growth of these microorganisms. Mini-splits operated in the cooling mode as well as portable and window air conditioners can also become contaminated with mold.
In new homes, it’s tragic how often the systems are contaminated by construction dust prior to occupancy; all you have to do is remove a floor register and look into a duct with a mirror and flashlight, to see the mess.
The furnace/air handler:
When humid summer air is cooled on the A/C coil, the air reaches its dew point, and moisture condenses on the cooling coils and is collected in drip pans. The water then either flows by gravity into drains or into condensate pumps that discharge the water to the exterior. If water accumulates in a drip pan when a drain line is clogged, the overflowing water can rust out and destroy the heat exchanger (if above a furnace), or drip into the blower cabinet and create damp conditions conducive to mold growth (particularly if exposed, dusty fibrous insulation is present).
Unfortunately, poor filtration is the rule rather than the exception. When biodegradable dust builds up on the cooling coil, the dust not only can block the flow of air but can also provide a substrate for biological growth as soon as the dust is dampened by condensed water. Lining material in the supply plenum (downstream from the coil) can also get moldy from water droplets entrained in the airflow or simply from the moisture-saturated air coming off the coil.
During your inspections, you may want to note if the cooling coil is accessible for inspection and cleaning. If you don’t include looking at mechanical equipment in your inspections, then you could recommend that your client have the air handler/furnace inspected, especially if your client has
allergies or asthma.
Here are some suggestions to offer your clients to help them keep an air handler/furnace clean:
- A/C coils and drip pans in central systems should be professionally inspected annually and cleaned
as needed. - There should never be water in the overflow pan, so during the cooling season, overflow pans should be checked, particularly if any pan is in the attic.
- The best filtration should be in place. I only recommend a pleated media filter with a MERV rating of at least at 8 (a MERV-11 for families with allergies). Electronic filters are rarely maintained as recommended. A dirty electronic filter is useless,
so I always recommend substituting a MERV-11 media filter for the electrodes; most manufacturers make a media filter that will fit into the holder.
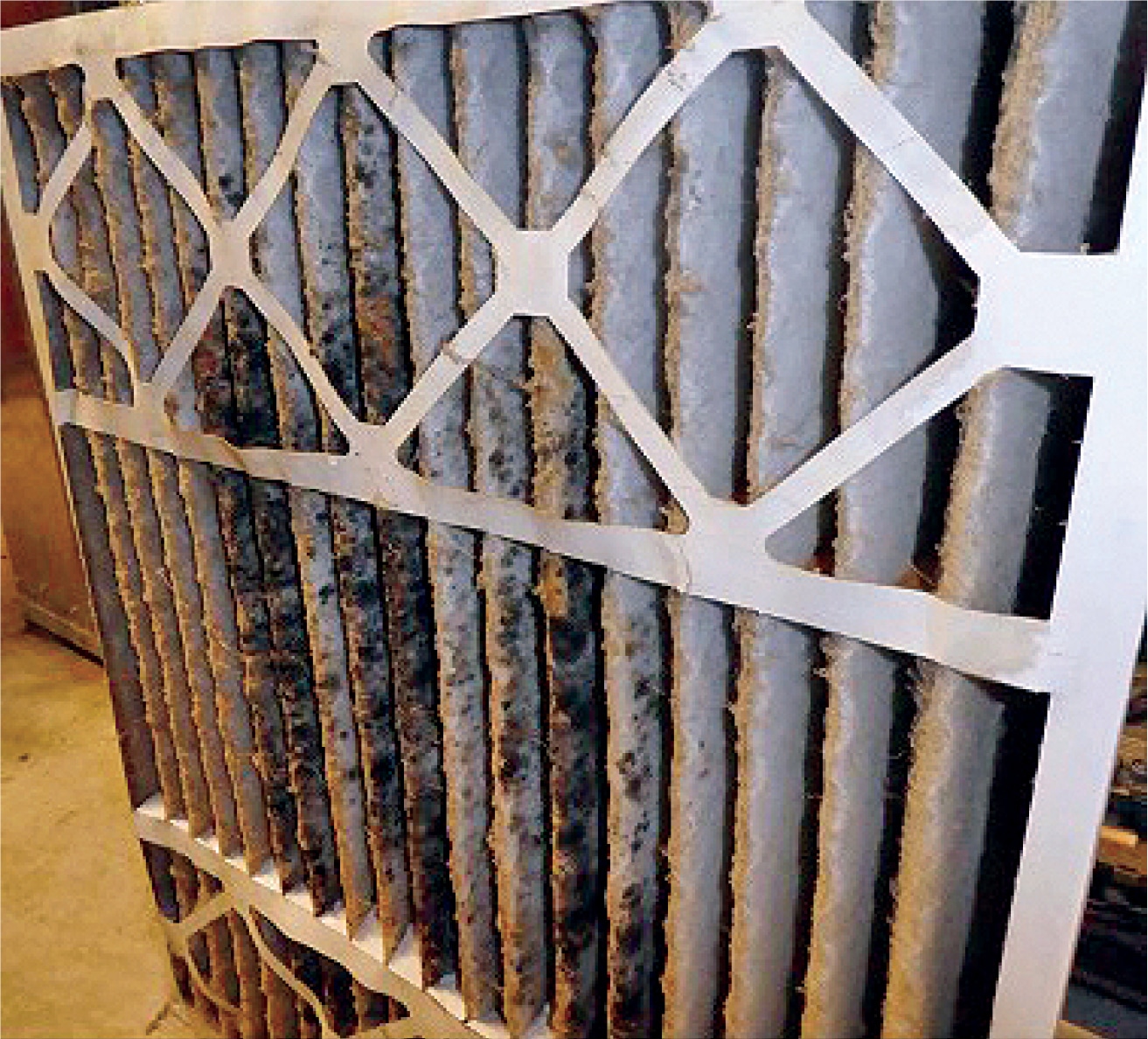
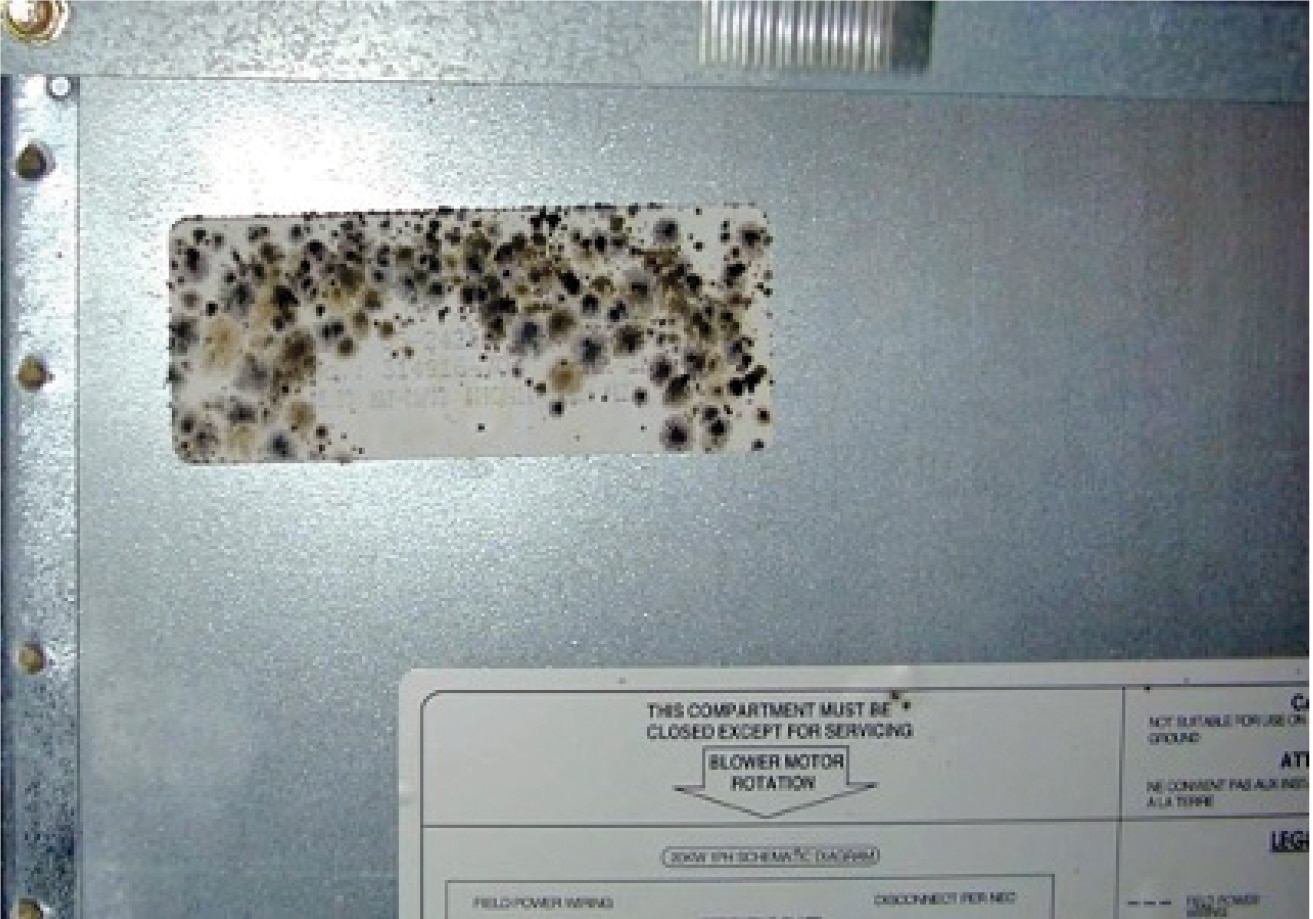
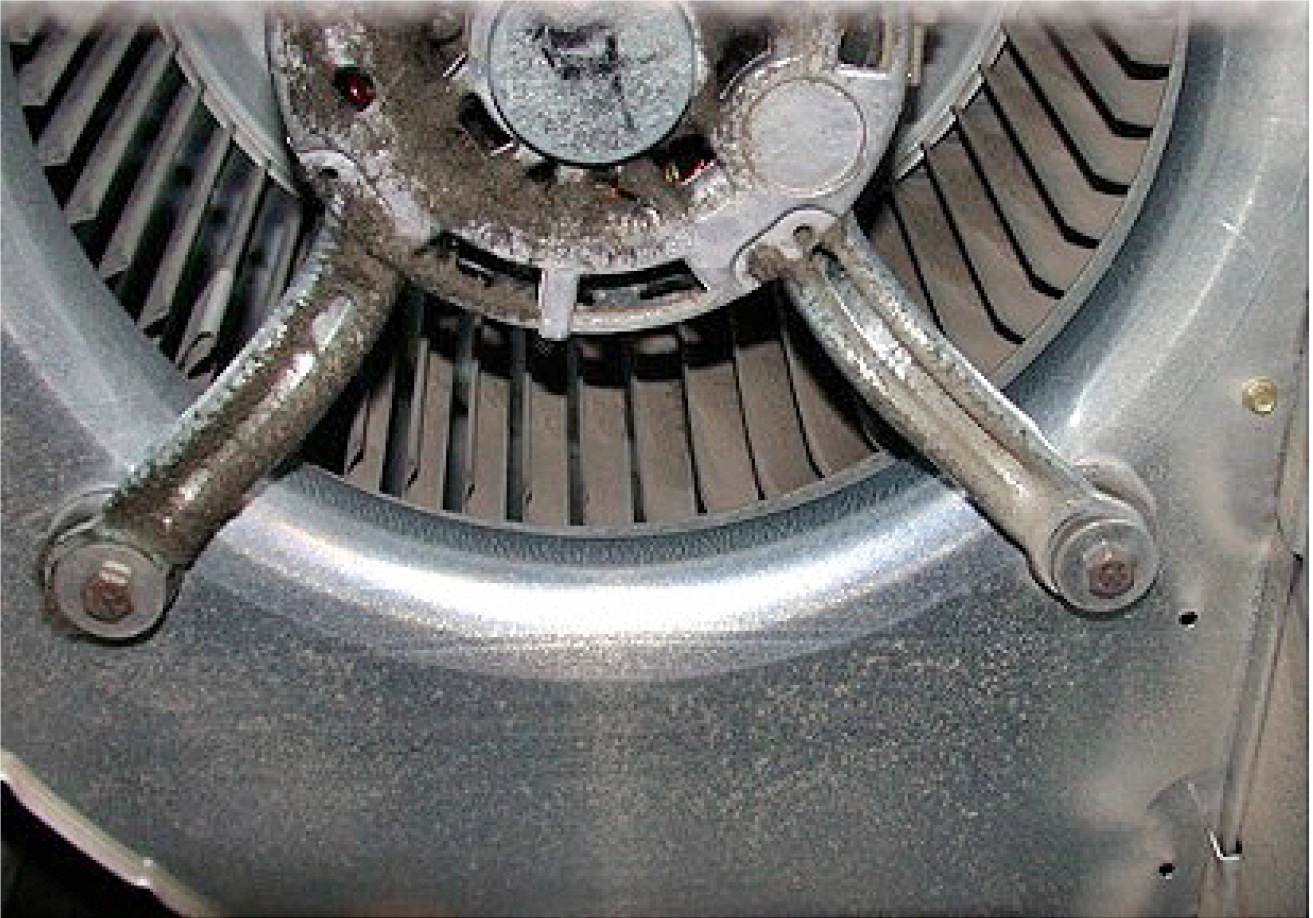
UV bulbs are not substitutes for efficient filtration.
A/C ducts:
If any ducted system was operated during construction or renovation, biodegradable dust (like sawdust) can soil the ducts. And sometimes occupants don’t even know that ducts should be inspected and cleaned as needed, whether the property is newly constructed or not.
Here are some suggestions to offer your clients to help them keep their ducts free of dust and other debris:
- Don’t settle for the cheap “blow and go” duct-cleaning job.
- Ducts that have been cleaned with brushes should only then have to be cleaned every 5 to 10 years; still, they should be inspected annually and cleaned more frequently as needed.
A filthy return duct
- Coarse pre-filtering material (MERV-3) behind return grilles can protect return ducts and help keep the system clean.
- If a house has a ducted A/C system but hot water, steam, or radiant heat, supplies and returns for attic-installed A/C systems should be closed during the heating season to prevent warm, moist air from migrating up into the system. Such air can lead to condensation and mold growth in the ducts or air handler. Solid material (even cardboard) can also be installed behind ceiling return grilles to prevent airflow from entering a return duct.
- A panned-bay return should be isolated from the basement and the rest of the floor cavity.
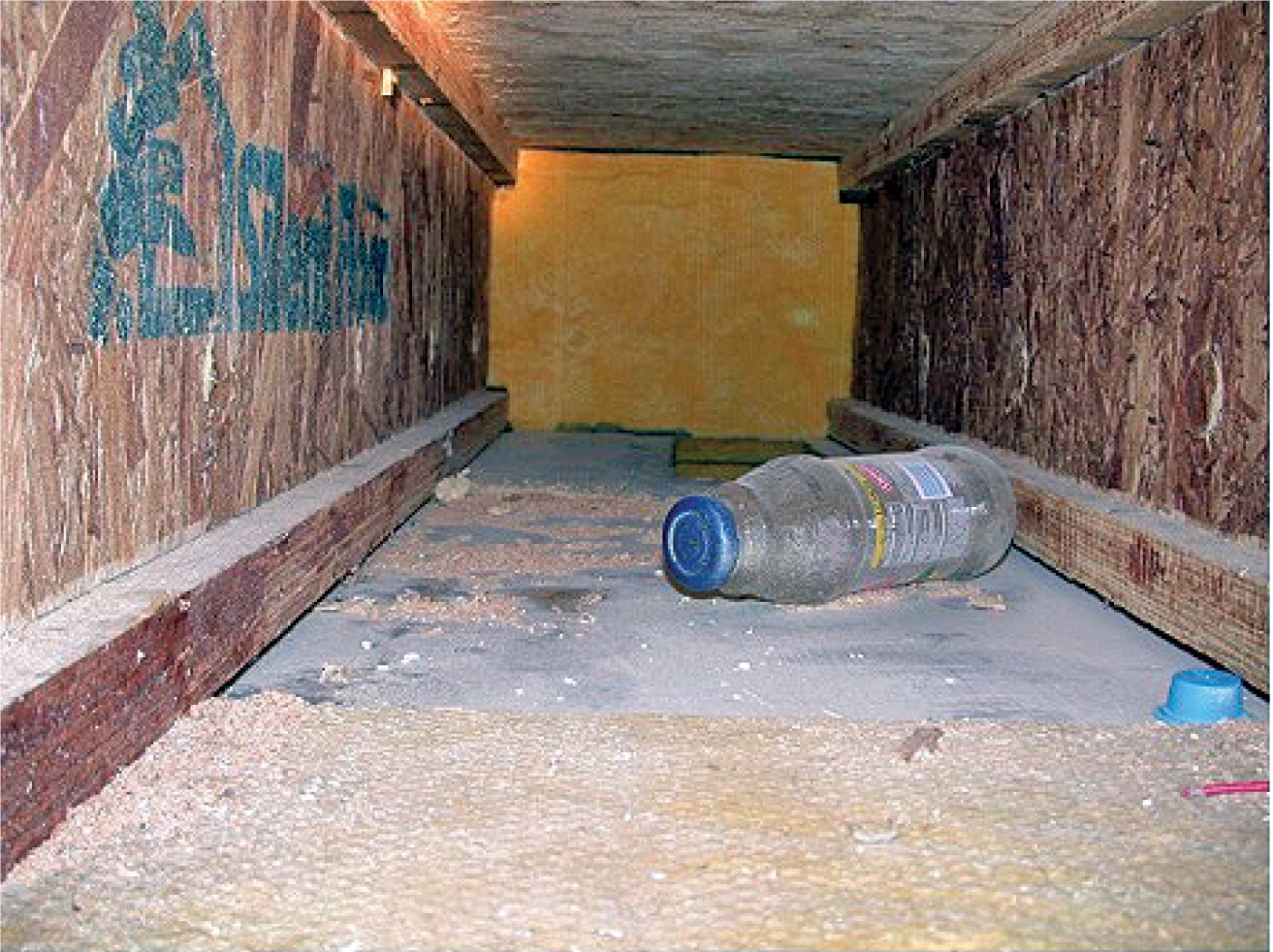
Mini-splits:
I am seeing more and more of these units in my investigations. They are a great way to add air conditioning in older homes that have radiator or baseboard heat. Unfortunately, though, mini-splits have inadequate filtration so inevitably become moldy, especially if they are only used in the cooling season.
One method of cleaning a mini split is to place a watertight plastic bag beneath the unit and to spray all the internal and external components with the appropriate cleaning product, and then to rinse the unit. If you are inspecting a house with one or more mini-splits, you could encourage your client to confer with an HVAC technician about cleaning options, especially if you see black spots on the louvers or in the dust on the blower blades (look carefully at the blades when stationary with a flashlight). Such spots are usually mold growth.
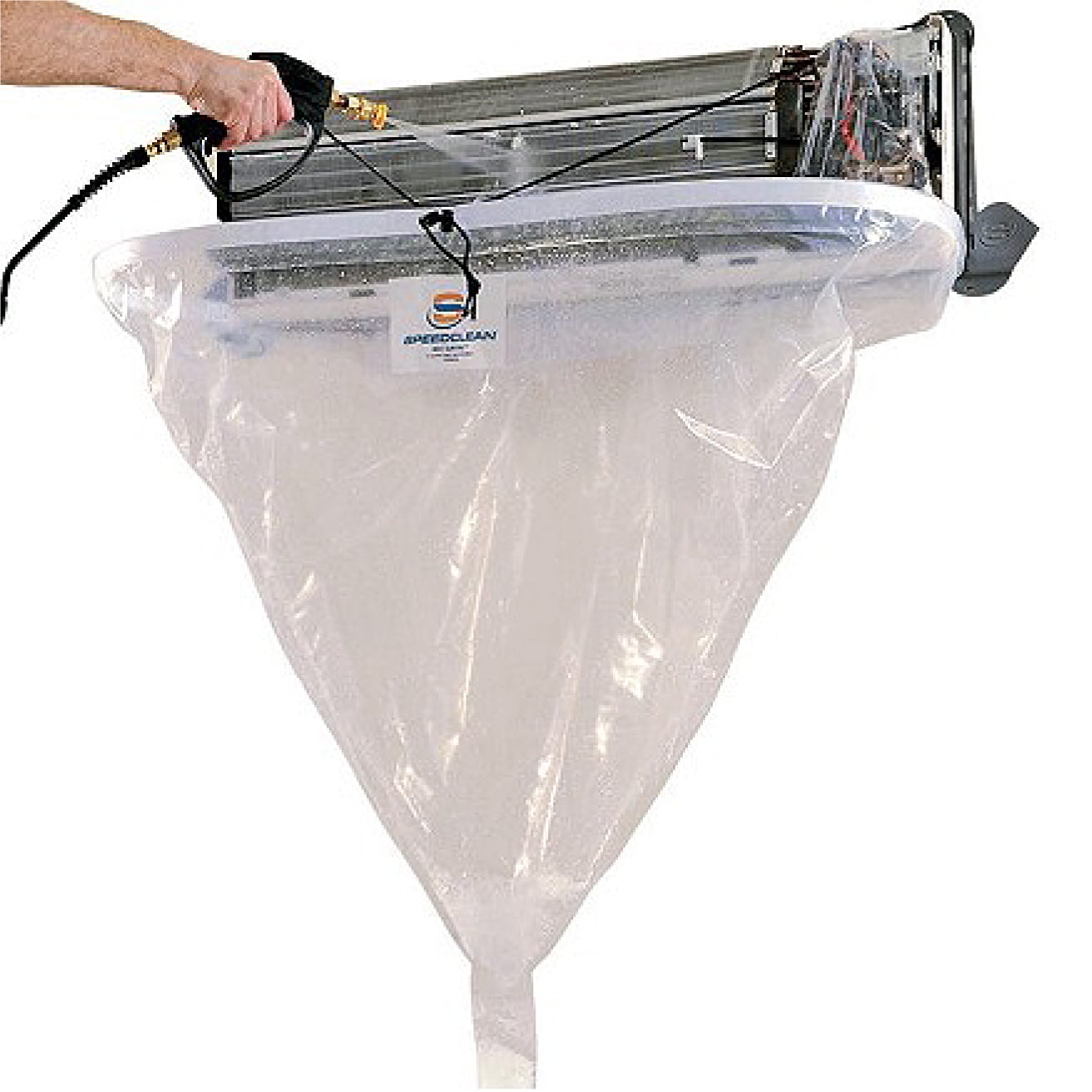
Window A/C units:
These are not immune from biological contamination, so they should be cleaned annually at the start of the cooling season rather than at the end of the cooling season, after which such units are often stored in damp garages and basements.

If the property you are inspecting has older wall or window air conditioners, it’s probably best if your client replaces these with new units.
Home inspectors aren’t always required to comment on indoor air quality issues; still, it seems worthwhile to give your clients information on how to maintain a healthy cooling system. And if you have concerns about the condition of such a system, recommend further evaluation.
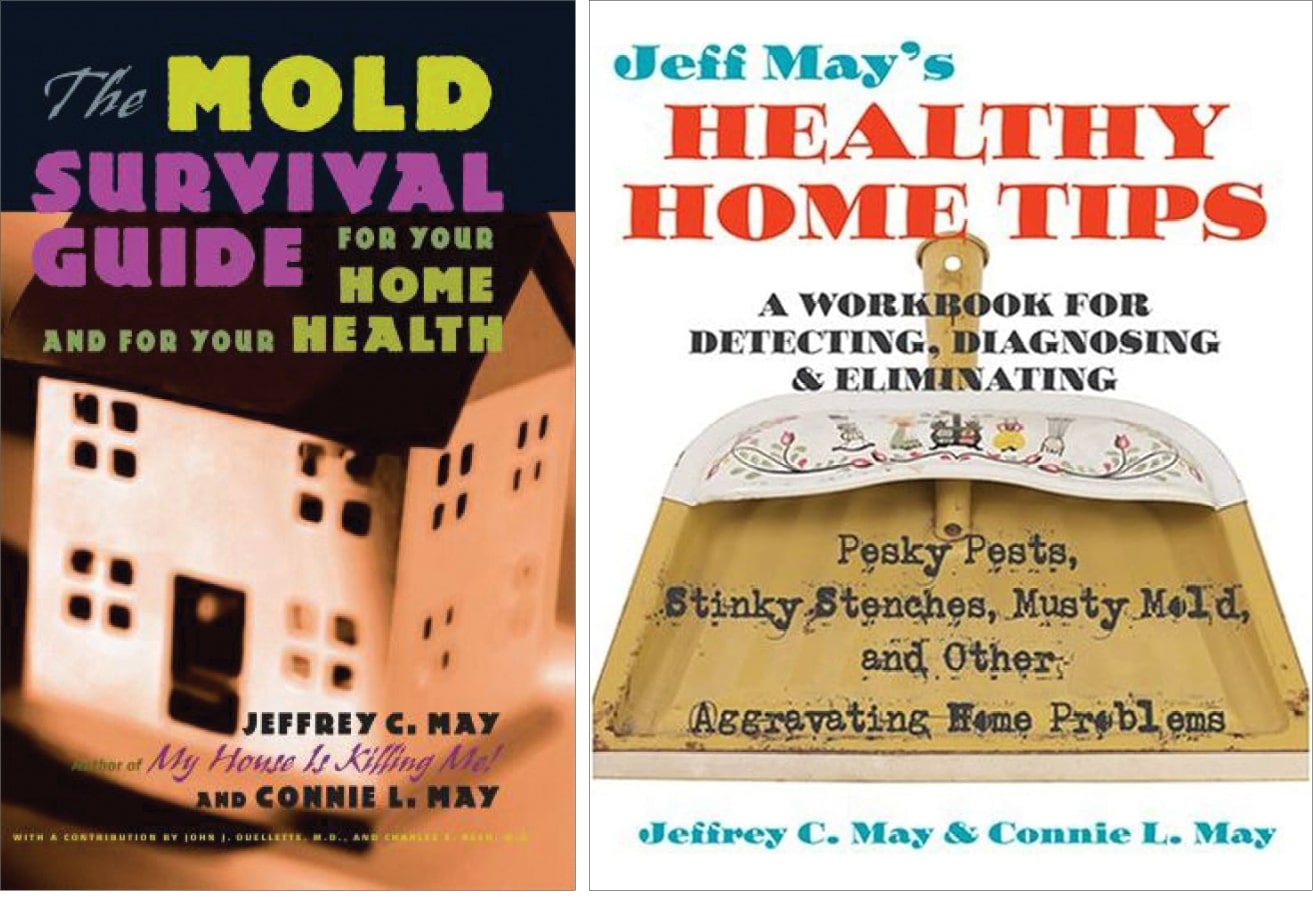
Tips on cleaning window A/C units are in our books The Mold Survival Guide: For Your Home and for Your Health, and Jeff May’s Healthy Home Tips, both published by
The Johns Hopkins University Press and available online.
Opinions or statements of authors are solely their own and do not necessarily represent the opinions or positions of ASHI, its agents, or editors. Always check with your local governmental agency and independently verify for accuracy, completeness, and reliability.
To Read the Full Article
ASHI offers its members unparalleled resources to advance their careers. ASHI offers training for inspectors at all levels of knowledge and experience, including resources about all major home systems. Members benefit from a vast network of experienced professionals, providing a community for mentorship and knowledge sharing..
In this Issue
Checking In
Celebrating ASHI Staff
How Do Home Inspectors Find Work?
Exploring the Lungs of the Home
What’s Your Difference?
Postcards from the Field
Advertisement
InspectorPro InsuranceFIND A HOME
INSPECTOR
Professional Networking
Grow your professional network, find a mentor, network with the best, and best part of the community that’s making home inspection better every day.
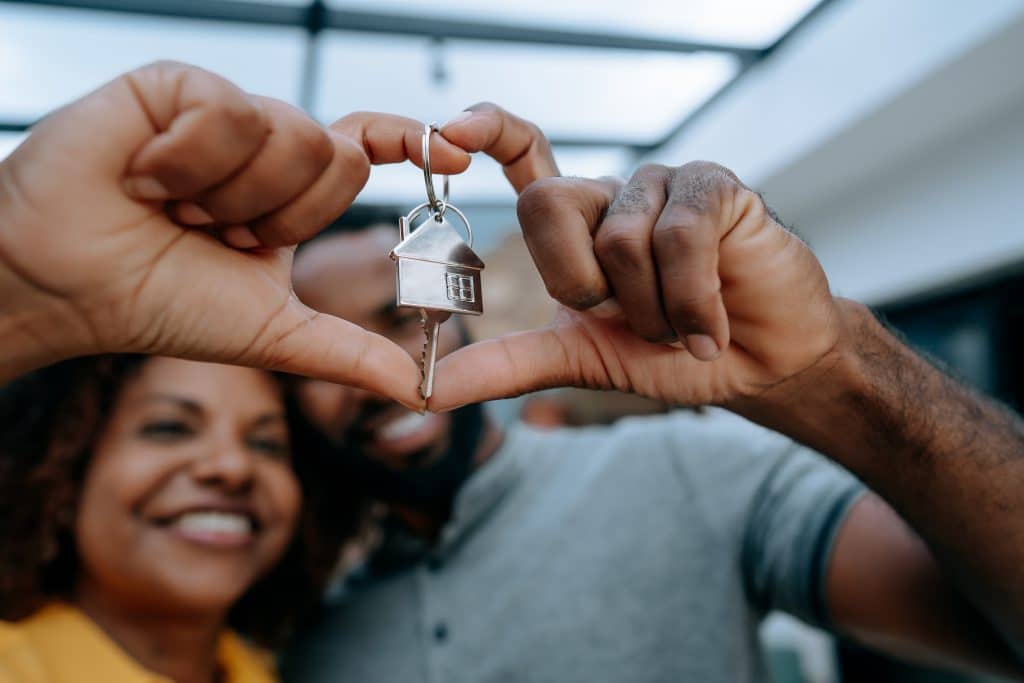