What Lurks in the Shadows?
HOME INSPECTIONS REQUIRE A SIGNIFICANT AMOUT of concentration to evaluate properly all of the pertinent systems. There are always distractions that can detour this concentration. These could be anything from a ringing cellphone (that is best left in the truck, if possible), an impatient Realtor, inquisitive children wondering why you are looking in their closet or a very interactive client, just to name a few. Couple any of these with a momentary “senior moment,” and you may forget why you are looking in the kids’ closet!
I thought I would just discuss a few issues that can be easily overlooked during the electrical system inspection.
We all see what I call B.I.L.W. far too often in the homes we inspect. This acronym stands for “brother-in-law wiring.” You know what I’m talking about; it usually resembles a back-lashed, bait casting fishing reel that was cast into a 30 mile-an-hour wind . . . wires going in all different directions and originating from a tangled mess! Homes with these installations put us on guard to carefully check everything.
But what about a neat installation in a panel with all circuits labeled, cable clamps in place and properly matched wire size to breaker size? The first thought is that all is well and maybe you won’t have to write an encyclopedia-sized concern summary. This is a welcome sight to any inspector and usually is an indication that a professional may have actually done the work. But don’t let your guard down. There could be concerns lurking in the shadows that are not so obvious.
I am just going to mention a few concerns that I see regularly and can be easily overlooked if you are not on your toes.
1. Look up—When inspecting the service, be sure to examine the condition of the service conductors at the point of attachment and also back to the utility pole. Many times these wires have cracked and are missing insulation and need replacement. This should be the responsibility of the power company to repair, but it is your client’s future home that could burn down if there is a fault.
2. Check HVAC sub panels—Many weekend electricians (a.k.a. brother-in-law) will add a circuit for a receptacle or light from an available circuit space in these panels. The trouble is, the HVAC system usually only needs a 240 volt circuit and does not have a neutral. “Brother-in-law’s” light and plug will work, but the supply grounding conductor is now carrying the neutral current for his marvelous installation and could be dangerous. Also check these panels for proper bonding. I see this missing on a regular basis.
3. Dryer circuits—I see this fairly often, particularly in 1950s and 60s homes. There is a 40 amp double-pole breaker with #6 stranded aluminum wires attached. No problem, right? Everything is compliant. But a closer look reveals that this is the dryer circuit. Okay, so what? Well, dryer receptacles are rated for 30 amps. The wiring and breakers are properly matched, but the weak link in the circuit is the receptacle. Simple fix: The breaker should be changed to a proper 30 amp breaker.
4. 30 amp single pole breakers—Most of the time this is a red flag in residences. There could be situations where this installation is correct for specialized circuits, but I have found that these are usually feeding receptacles and lights. “Brother-in-law” thought he could get more electricity by upsizing to 30-amp breakers! Same scenario as with the dryer circuit. Most standard receptacles and switches are rated for 15 or 20 amps, so even if the wiring is sized appropriately, the weak link is the outlet device.
5. Service panel upgrades—Many homes have electrical service upgrades to handle the increasing demand for power in today’s world. This is a valuable improvement when done properly. Unfortunately, far too often, only part of the upgrade is completed. I have seen homes upgraded from 100-to 200-amp services with new panels, new larger service entrance conductors, and run it all through the old 100-amp-rated meter base. Again, the weak link in the system. Always check the meter base when upgrades have been done. These are usually bootleg jobs with no permit or inspection.
6. Bootleg or false grounds—We all see older homes that have been remodeled and have 3-prong receptacles with no grounding conductor. This goes in the report as a defect and recommendations for correction. But what if your neon tester shows a proper ground on all of the receptacles and when you open the main panel, there are only one or two or maybe no circuits at all returning to the panel with grounding conductors? It checked okay, so what’s up? At this point, we have thrown brother-in-law under the bus so much he has more tire tracks on him than a 1960s drive-in parking lot, so we’re not going to blame him. This is usually the work of an experienced but dishonest electrician. This guy knows he can put a jumper on the receptacle to connect the ground screw to the neutral and “fool” the inspector’s little pocket tester. Shame on him! If all of the receptacles test okay and there aren’t enough grounding conductors in the panel, check a little further. There could be an improper ground connection to a water pipe. Maybe remove a cover or two and look for the jumper or invest in a circuit analyzer that will detect the false grounds. They are a little pricey but worth the investment in my opinion.
The old saying goes, “Don’t judge a book by its cover.” This is a good rule to live by when inspecting homes. All is not always as it seems.
To Read the Full Article
ASHI offers its members unparalleled resources to advance their careers. ASHI offers training for inspectors at all levels of knowledge and experience, including resources about all major home systems. Members benefit from a vast network of experienced professionals, providing a community for mentorship and knowledge sharing..
In this Issue
FIND A HOME
INSPECTOR
Professional Networking
Grow your professional network, find a mentor, network with the best, and best part of the community that’s making home inspection better every day.
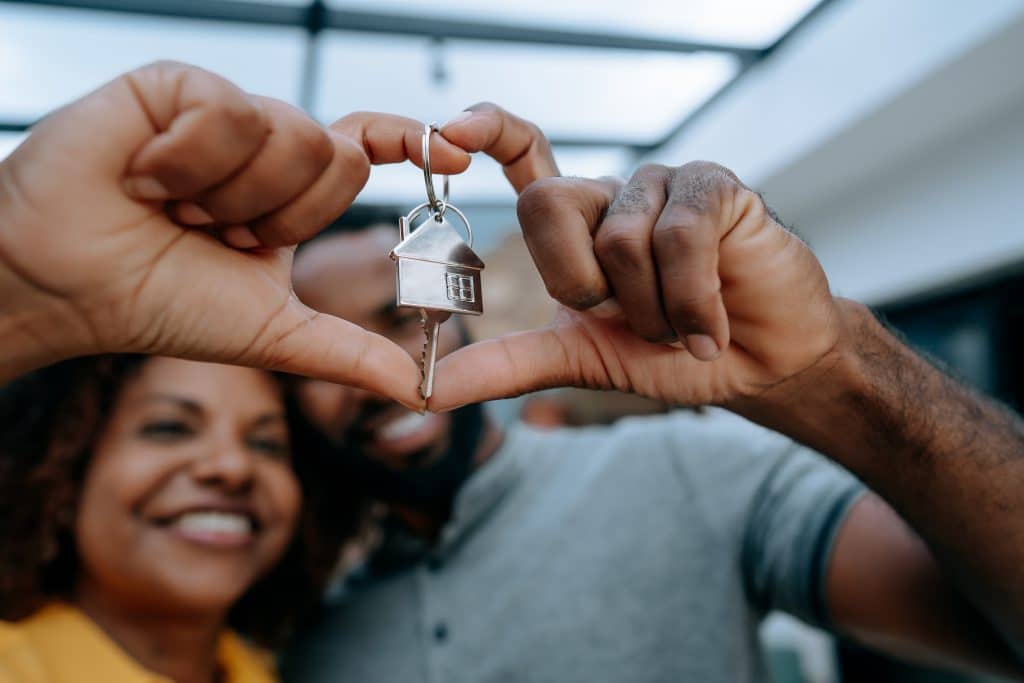