Problem Drywall: Study of Health Effects Continues
CPSC Updates Remediation Recommendations & Winds Down Scientific Investigation
Key Concepts
- No link found between exposure to problem drywall and deaths of 11 people who had previously lived or visited homes reported to contain it.
- Centers for Disease Control asked to undertake comprehensive study of possible long-term health effects.
- CPSC/HUD drop recommendation to remove electrical wiring in homes with problem drywall after study finds no evidence linking the drywall to safety hazards in home electrical systems, but continue to recommend replacing five other components.
- Installation years broadened to include 2009.
No link between problem drywall and 11 reported deaths
There is no evidence linking exposure to problem drywall and 11 reported deaths, according to the Centers for Disease Control and Prevention’s (CDC) National Center for Environmental Health. Its review, published in March 2011, confirms the results of previous reviews conducted by the U.S. Consumer Product Safety Commission (CPSC).
Nevertheless, the CPSC, which is in the final stages of completing its scientific investigation into problem drywall, has requested that the CDC consider undertaking a comprehensive study of any possible long-term health effects.
The center’s review, which had been requested by CPSC, summarizes investigations by state public health authorities of the available medical records of 11 people who died and had previously lived in or visited homes reported to contain problem drywall. State public health authorities concluded that problem drywall was not a factor in the deaths.
CPSC and HUD issue updated remediation protocol for homes with problem drywall
CPSC also received a study conducted on its behalf by Sandia National Laboratories, which finds no evidence of a safety hazard to home electrical systems from the problem drywall.
Sandia simulated long-term exposure of wiring and other electrical components to hydrogen sulfide gas, which is associated with problem drywall.
Based on this study, CPSC and HUD staff, representing the Interagency Task Force on Problem Drywall, are no longer recommending the removal of all electrical wiring in homes with problem drywall. This change in the government’s protocol may reduce the cost of remediation for many homes.
After simulating more than 40 years of corrosive conditions that could exist in problem drywall homes, Sandia staff did not observe any acute or long-term electrical safety events such as smoking or fire. Corrosion and blackening of the exposed electrical components did occur and was observed to be consistent with the characteristic corrosion reported to CPSC by thousands of consumers. Based on this study, it is the belief of the staffs of CPSC, HUD and Sandia that long-term exposure of wiring and other electrical components to hydrogen sulfide gases does not indicate a safety hazard to a home’s electrical systems.
With these changes, the remediation guidance for homes with problem drywall calls for the replacement of all:
– problem drywall;
– fire safety alarm devices, including smoke and carbon monoxide alarms;
– electrical distribution components, including receptacles, switches and circuit breakers; and
– gas-service piping and fire suppression sprinkler systems.
Revised identification guidance
In another change, the CPSC broadened the range of installation years to include homes where drywall was installed as late at 2009.
Previously, it was believed all such problem drywall was installed by the end of calendar year 2008. In this updated Identification Guidance for Homes with Corrosion from Problem Drywall, as of March 18, 2011, the years of installation are adjusted accordingly to include calendar year 2009 because some of the drywall imported in the earlier years was not installed until 2009. This guide continues to represent what the Federal Interagency Task Force on Problem Drywall believes is the best approach based upon the information available today.
Identification method
The identification process requires two steps: (1) an initial or threshold inspection to find visual signs of metal corrosion and evidence of drywall installation during the relevant time period, and (2) the identification of corroborating evidence or characteristics.
Step 1: Threshold inspection
Visual inspection must show:
(a) Blackening of copper electrical wiring and/or air conditioning evaporator coils; and
(b) The installation of new drywall (for new construction or renovations) between 2001 and 2009.
A positive result for the first step (including both criteria) is a prerequisite for any further consideration.
Rationale
A visual observation of corroded air conditioning evaporator coils and/or electrical wiring by trained inspectors is believed to be a prerequisite for consideration of a home as having problem drywall. The Florida Department of Health long has included such corrosion as part of its definition of problem drywall homes. It is appropriate to limit the dates of installation to the relevant time period because this corresponds to the majority of complaints received by the CPSC. In addition, older homes with earlier dates of installation could exhibit corrosion due to different sources acting over longer periods of time.
A CPSC contractor completed a detailed study of 51 homes in Alabama, Florida, Louisiana, Mississippi and Virginia. The report was issued November 23, 2009, and is available on www.drywallresponse.gov. This investigation included inspections of each home for the presence and extent of corrosion. Copper and silver metal test strips, called “coupons,” were placed in each home for two weeks to test the corrosive environment. The copper and silver coupons showed significantly higher rates of corrosion in homes where complaints had been registered than in the control homes. The dominant types of corrosion on the coupons were copper sulfide and silver sulfide, respectively, as determined by additional laboratory tests. Copper sulfide and silver sulfide appear as a black coating on copper or silver metal. Visual inspection and evaluation of electrical (ground) wire corrosion also revealed statistically significant greater corrosion in complaint homes compared to the control homes.
Step 2: Corroborating evidence
Because it is possible that corrosion of metal in homes can occur for other reasons, it is important to obtain additional corroborating evidence of problem drywall. Homes with the characteristic metal corrosion problems also must have at least two of these corroborating conditions if the new drywall was installed between 2005 and 2009. For installations between 2001 and 2004, at least four of the following conditions must be met:
(a) Elemental sulfur levels in samples of drywall core found in the home exceeding 10 ppm;
(b) Corrosive conditions in the home, demonstrated by the formation of copper sulfide on copper coupons (test strips of metal) placed in the home for a period of two weeks to 30 days or confirmation of the presence of sulfur in the blackening of the grounding wires and/or air conditioning coils;
(c) Confirmed markings of Chinese origin for drywall in the home;
(d) Elevated levels of hydrogen sulfide, carbonyl sulfide and/or carbon disulfide emitted from samples of drywall from the home when placed in test chambers using ASTM Standard Test Method D5504-08 or similar chamber or
headspace testing; and
(e) Corrosion of copper metal to form copper sulfide when copper is placed in test chambers with drywall samples taken from the home.
Collecting evidence of these corroborating conditions, in some cases, will require professional assessors and/or testing by analytical laboratories.
Rationale
The Federal Interagency Task Force’s study of the elemental and chemical composition of 17 drywall samples shows higher concentrations of elemental sulfur and strontium in certain Chinese drywall than in non-Chinese drywall. Although, the 51-home study (41 homes with reported problems and 10 control homes) also found a correlation between elevated strontium levels and problem homes, additional testing conducted on a wide range of drywall samples found that the use of strontium as a marker resulted in false-positives where some non-problem drywall samples (based on chamber testing) were found to contain elevated strontium levels.
The task force does not believe strontium has a causative role, and, in light of the possibility for false-positives, it no longer considers elevated strontium levels to be valid corroborating evidence for problem drywall. However, in many cases, screening for strontium can be an effective tool in identifying what boards may warrant additional testing for elemental sulfur. The additional testing in the contractor’s draft report found that elemental sulfur (also known as orthorhombic sulfur) was highly correlated with problem drywall. Thus, the presence of elevated levels of elemental sulfur is believed to be corroborating evidence for homes with problem drywall.
The 51-home study and the preliminary corrosion reports also found that the type of corrosion present on copper coupons, copper electrical wire and air conditioning evaporator coils was copper sulfide. Thus, the confirmation of copper sulfide or sulfur in the corrosion of the copper (and similarly, silver sulfide or sulfur in the corrosion on silver coupons) is believed to be a corroborating marker. Chinese drywall installed in the identified period has been associated with the types of corrosion problems reported. This does not imply that all Chinese drywall, or that only Chinese drywall, is associated with these problems, but that among homes with the characteristic corrosion, Chinese drywall is a corroborating marker. It is not absolutely necessary for the markings to be found because, in some cases, Chinese drywall does not have markings that identify the nation of origin of the drywall.
Additionally, the preliminary results re-ported for the study under way at the Lawrence Berkeley National Laboratory indicated that higher levels of total volatile sulfur compounds were released by Chinese drywall samples compared to domestic drywall samples, and the 51-home study reported an association between hydrogen sulfide levels in homes and corrosion in those homes. Thus, it is believed that one of the possible corroborating tests that could be considered is emissions testing from suspect drywall from homes. Another similar corroborative test that could be considered is determining if corrosion of copper metal to form copper sulfide occurs when copper is placed in test chambers with drywall from the home at elevated humidity. Chamber tests may be costly and time-consuming options.
More information
More information on problem drywall is available at the federal Drywall Information Center website, www.drywallresponse.gov.
The U.S. Consumer Product Safety Commission is charged with protecting the public from unreasonable risks of injury or death from thousands of types of consumer products under the agency’s jurisdiction. To report a dangerous product or a product-related injury, call CPSC’s Hotline at 800-638-2772 or CPSC’s teletypewriter at 301-595-7054. To join a CPSC email subscription list, go to www.cpsc.gov/cpsclist.aspx. Consumers can obtain recall and general safety information by logging on to CPSC’s website at www.cpsc.gov.
HUD’s mission is to create strong, sustainable, inclusive communities and quality affordable homes for all. More information about HUD and its programs is available on the Internet at www.hud.gov and www.espanol.hud.gov.
————————————————————
FTC Warns Public: Don’t Get Nailed by Bogus Drywall Tests and Treatments
The Federal Trade Commission (FTC) says homeowners should be on the alert for anyone trying to sell test kits, inspections and quick fixes for tainted drywall. You can learn more about the federal government’s drywall investigation, and sign up for email alerts, at www.drywallresponse.gov. To file a complaint, consumers should visit the CPSC at www.cpsc.gov/cgibin/drywall.aspx, call 800-638-2772 or email, info@cpsc.gov.
The FTC works for the consumer to prevent fraudulent, deceptive and unfair business practices in the marketplace and to provide information to help consumers spot, stop and avoid them. To file a complaint or to get free information on consumer issues, visit ftc.gov or call toll-free, 877-FTC-HELP (877-382-4357); TTY: 866-653-4261. The FTC enters consumer complaints into the Consumer Sentinel Network, a secure online database and investigative tool used by hundreds of civil and criminal law enforcement agencies in the United States and abroad.
————————————————————
To Read the Full Article
ASHI offers its members unparalleled resources to advance their careers. ASHI offers training for inspectors at all levels of knowledge and experience, including resources about all major home systems. Members benefit from a vast network of experienced professionals, providing a community for mentorship and knowledge sharing..
In this Issue
FIND A HOME
INSPECTOR
Professional Networking
Grow your professional network, find a mentor, network with the best, and best part of the community that’s making home inspection better every day.
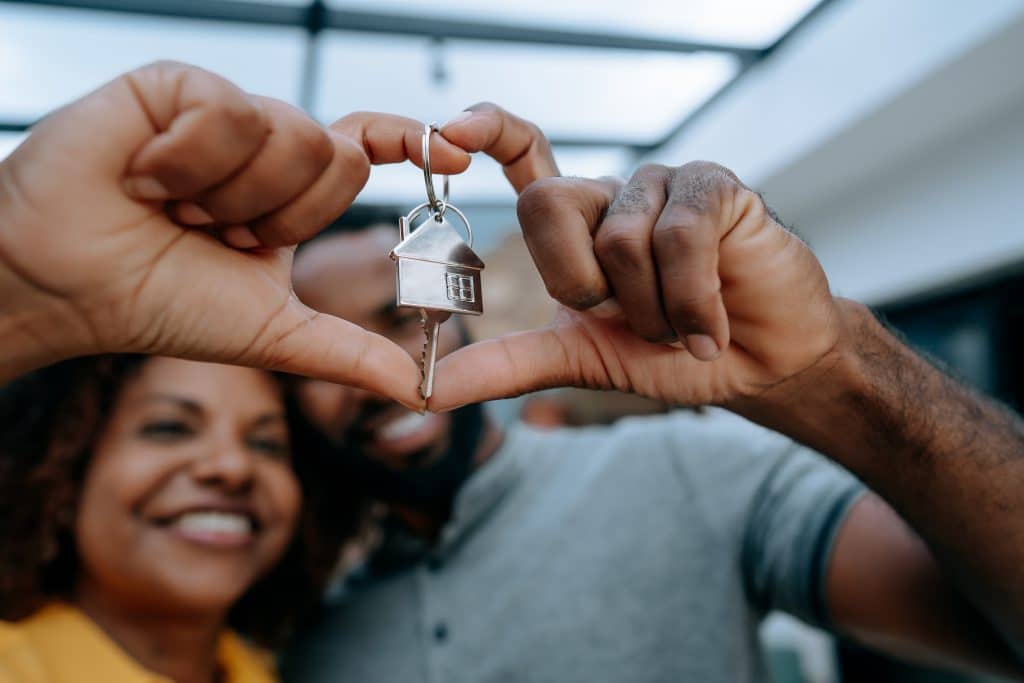