Grounding and Bonding: What Home Inspectors Need to Know
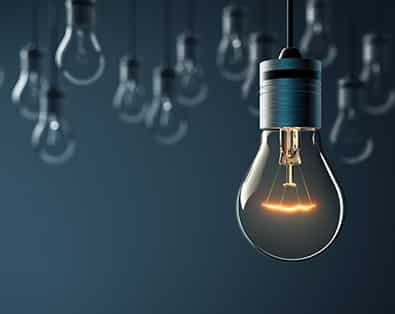
Probably the most confusing part of an electrical system for home inspectors to grasp is the proper implementation of grounding and bonding requirements. Numerous magazine articles, group chat forums and social media discussions have all made attempts to explain the “what, why, where and how” of grounding and bonding.
In this article, I will try to simplify this subject as it relates to a home inspection.Hope I can clarify some things and not further “muddy the waters!”
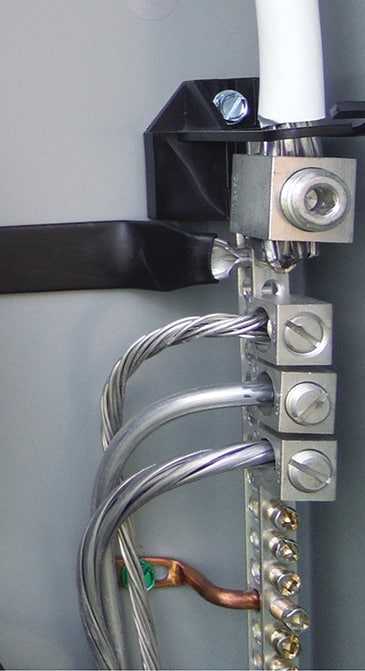
Definitions and Explanations
First, let’s review the basic definitions of grounding and bonding.
Grounding/grounded
Connecting/connected to ground or to a conductor that extends the ground connection.
Bonding/bonded
Connecting/connected to establish electrical continuity and conductivity.
So, to be grounded, there must be a direct connection to the earth (that is, the ground). To be bonded, there must be a direct connection to another conductive device or material. Both of these types of connections are done by design in electrical systems for safety. Unintentional grounding and bonding can be present in certain situations that can cause faults and hazards. I will give examples of these later in this article.
A primary purpose of grounding an electrical system is to limit voltage from lightning and power surges, and to direct that potentially dangerous energy to the earth. Bonding is done to connect all conductive electrical equipment to keep the equipment at an equal electrical voltage potential and to provide a path back to the power source through an overcurrent protective device that will de-energize the circuit in the event of a fault. The equipment grounding conductor (EGC) provides that path.
Equipment grounding conductor (EGC)
The conductive path used to carry ground-fault current and used to connect normally non-current–carrying metal parts of equipment together.
Now, by that description, we see that the EGC has at least two purposes: as a designed fault current path and to “bond” conductive equipment. Yes, I said “bond.” This is where some confusion can come in. Although we refer to these conductors as “grounds,” “grounding wires” and equipment grounding/grounds,” they are also bonding conductors.
EGCs can be either wires or metal raceways between panel enclosures and boxes. The origin of the EGC is at the service equipment, where it is connected to the system grounded conductor (service neutral) or the grounding electrode conductor or both.
Grounding electrode conductor (GEC): A conductor used to connect the system-grounded conductor or the equipment to a grounding electrode or to a point on the grounding electrode system.
The GEC is connected to the system neutral. This connection could be in the service equipment panel, the meter base or at the load end of the overhead service drop (the connection to the utility).
Grounded Conductor
A system or circuit conductor that is intentionally grounded.
The neutral conductor in a standard residential system is a grounded conductor.
Please note: Not all “grounded conductors” are neutrals. There are systems where a phase conductor is intentionally grounded in industrial applications and they are not “neutrals.”
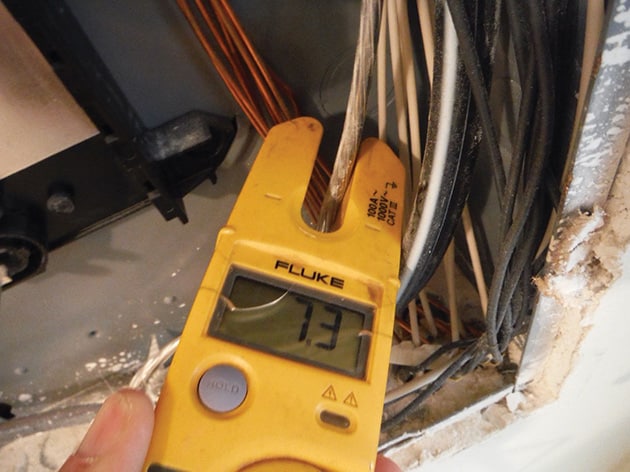
For our purposes in this discussion, the neutral is the grounded conductor.
Although the neutral, EGC and GEC are all grounded, they have different and specific functions. If you don’t remember anything else from this information, remember and understand this:
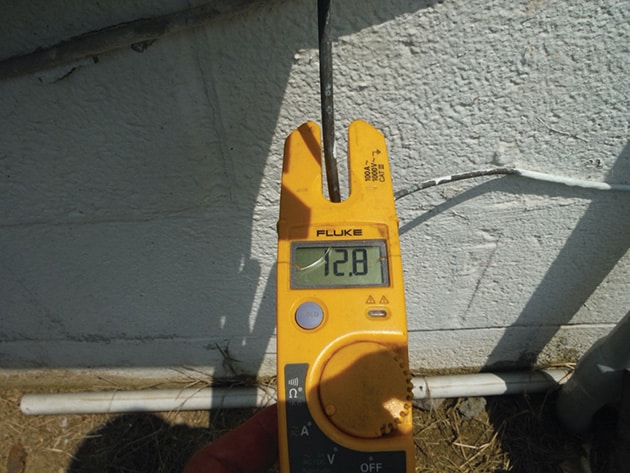
In a normally operating electrical system, the neutral (grounded conductor) carries current by design. The EGC and GEC only carry current in the event of a ground fault or improper load side bond.
More Terms That May Confuse Inspectors
The neutral conductor must be “bonded” at the service equipment. This is known as “supply-side bonding” because it is done on the line side of the service disconnect. Supply-side bonding includes the connection of the neutral conductor to the service enclosure, the GEC, the equipment grounding conductor and to the service raceway (conduit) if it is metal. This connection ensures that the neutral and all conductive electrical equipment are at an equal voltage potential to ground. The “main bonding jumper” makes the connection of the service neutral to the service enclosure. The main bonding jumper could be a screw that threads into a designated tapped hole in the panel enclosure or it could be a listed strap that connects the neutral bus to the enclosure.
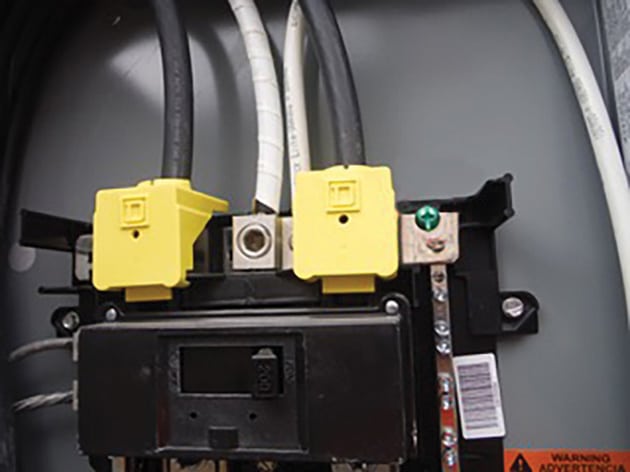
After this point of connection/bonding, the neutral conductor is required to be separated from the metallic, conductive components and equipment in the system. So, at downstream panels, outlets, devices, metal boxes and disconnects, the neutral is no longer allowed to be “bonded.”
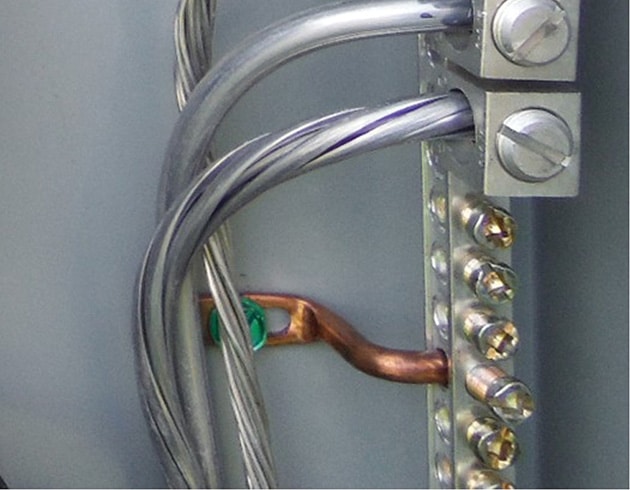
This is where I often see confusion and arguments among home inspectors. A commonly incorrect statement is as follows: “A subpanel should not be bonded.” While it is true that the neutral should not be bonded in a subpanel, the panel enclosure must certainly be bonded. This bond is provided through the equipment grounding system that we discussed earlier.
There is a Distinct Difference Between the Neutral Being Bonded and the Panel Enclosure Being Bonded.
Past installation practices allow exceptions to load side neutral bonding in some situations. The metal chassis of electric dryers and ranges were allowed to have the neutral conductor bonded on the older method of three wire circuits to these appliances. This is no longer allowed in new installations.
Feeders to separate buildings also allowed three wire installations. The neutral in those feeds were required to be bonded to the subpanel enclosure, and to the EGC and GEC systems at the separate building. The building must have its own grounding electrode system. There could be no other conductive path between the buildings for this to be compliant. This provision is no longer allowed (per the 2008 NEC) except for existing installations. Four-wire feeds are now required with separate neutrals and EGCs.
Rationale for Rules and What to Look for in the Field
Equipment bonding is required to keep all normally non-current–carrying conductive devices at an equal voltage potential. That bonding is done through the equipment grounding system to provide a dedicated low-impedance path back to the overcurrent protective device to clear a fault.
Separating the neutral and equipment grounding conductors after the service disconnect is required to prevent current from using the metal components as a parallel path. Remember that current will take ALL available paths. If the neutral is bonded to the metal enclosure of a subpanel, that panel would be part of the circuit and would be energized with the neutral current. The same is true with metal boxes, metal frames of appliances, switches and receptacles. All of these metal components or devices are located throughout the home and are “touchable objects.”
These photos show how the current is affected when the neutral is bonded in a subpanel, compared with when it is not bonded. The feeder circuit is under the same load in both examples.
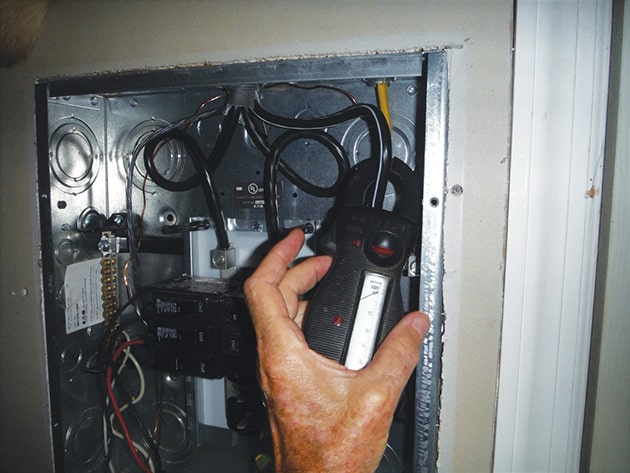
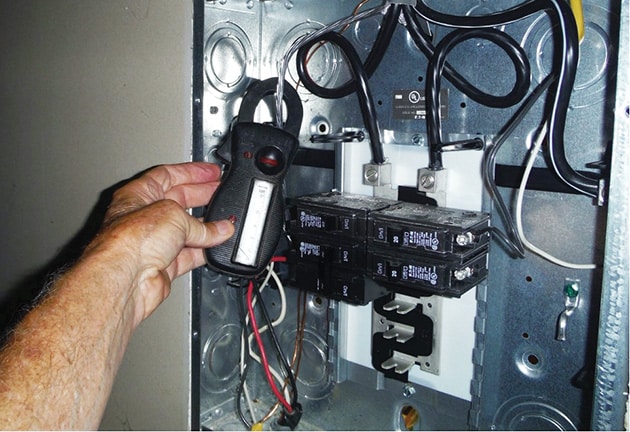
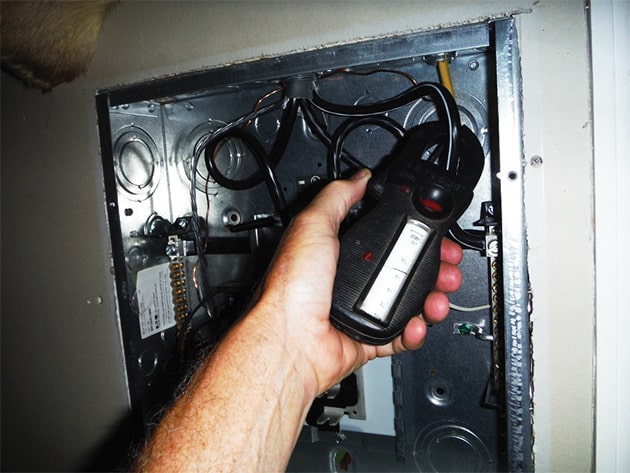
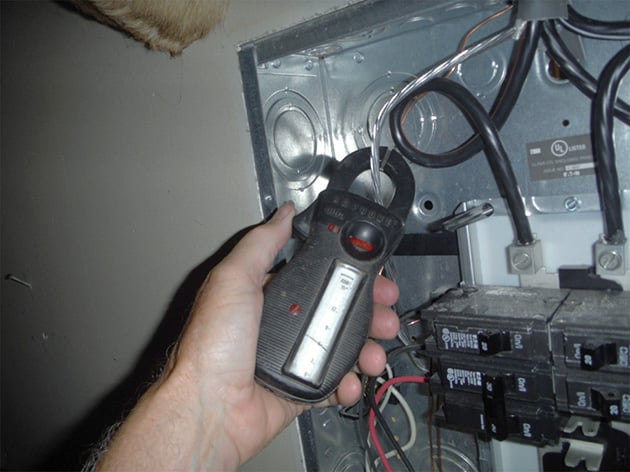
Why Do We Bond the Neutral and EGCs at the Service Equipment?
The service neutral is the path back to the electrical supply source, which is the service transformer. We want that path to be low impedance to allow fault current to rise as rapidly as possible to a level that will trip a breaker or blow a fuse.
If we continued to separate them at this point, the fault current would travel through the grounding electrode system to the earth. The fault current would still try to return to the source through the earth, but the earth is typically high resistance/impedance and is not an effectively conductive path. Due to the high resistance, the fault current will not rise to a level sufficient to trip a breaker or blow a fuse and the fault will not clear.
Grounding and bonding must work together in order to provide a safe system. Having one without the other defeats the intended result.
Real-life Example of an Electrical Supply Being “Bonded,” but not “Grounded”
A three-wire feeder was run to a subpanel in a detached garage. The feeder consisted of two hot conductors and an insulated neutral conductor. The neutral was terminated on an insulated “floating” neutral bar in the subpanel. The branch circuit equipment grounding wires were terminated to the grounding bar that was directly attached to the panel enclosure; so, the neutrals and equipment grounds were “separated.” The branch circuit equipment grounding wires were “bonded” to the metal outlet boxes and metal fluorescent light fixture enclosures throughout the garage. These metal boxes and fixtures were fastened to the metal siding in the garage.
As I began my inspection of the garage electrical system, I touched the panel cover to open it and felt a definite shock. I pulled out my non-contact voltage sensor and checked the panel, which indeed was energized.
(Please note: Best practice would have been to check with the sensor first!)
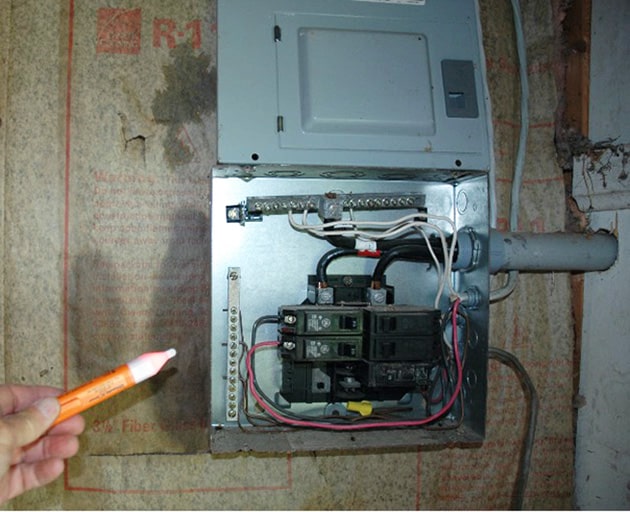
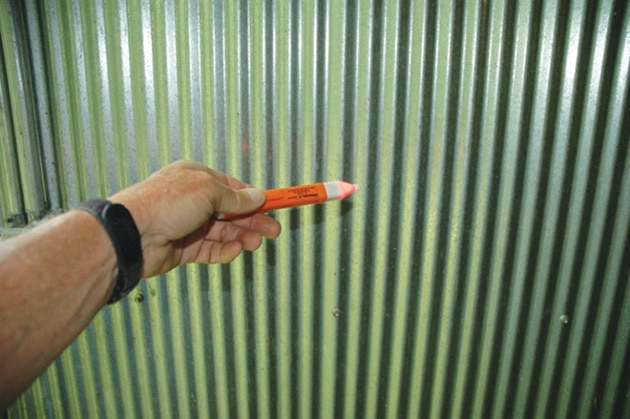
The owner of the home was present during this incident and confessed that he had done all of the wiring. He started checking some light fixtures as I continued with my inspection. After a short time, he asked me to come back to the garage. He had found a hot wire that had come loose in one of the fluorescent fixtures and was contacting the metal enclosure. That wire then energized all of the metal components and siding via the bonding connections.
There was no equipment grounding conductor with the feeder to the garage and the feeder neutral was separated from the equipment grounds so, there was no path for the fault current to trip the feeder circuit breaker. The components of the system were “bonded,” but they were not “grounded.”
The metal boxes, panel, light fixtures and metal siding measured 118 volts to the neutral! Since I was standing on a dirt floor when I touched the panel, the current used me and the earth as a path to complete the open circuit and return to the supply source. Fortunately, that was a high- resistance/poor-conductive path and allowed only a very minimal current flow (but enough for me to feel the shock).
As I mentioned earlier, 3-wire feeders to detached buildings were at one time allowed by the NEC. Again, these 3-wire installations require bonding the neutral and EGC.
Had the garage in my inspection been properly wired for a 3-wire supply, the fault current would have used the neutral feeder conductor and tripped the breaker.
Low-voltage systems such as cable TVs and telephones must also be bonded to the grounding electrode system. This connection is done at the intersystem bonding terminal.
Be Watchful on Your Inspections
Unfortunately, improper grounding and bonding installations are very common. Home inspectors encounter these potentially dangerous issues almost every day. Knowing the basic logic for specific requirements will help inspectors to understand the concerns, explain the consequences and identify defects when they are present.
I hope the “muddy water” is maybe a little clearer now.
To Read the Full Article
ASHI offers its members unparalleled resources to advance their careers. ASHI offers training for inspectors at all levels of knowledge and experience, including resources about all major home systems. Members benefit from a vast network of experienced professionals, providing a community for mentorship and knowledge sharing..
In this Issue
FIND A HOME
INSPECTOR
Professional Networking
Grow your professional network, find a mentor, network with the best, and best part of the community that’s making home inspection better every day.
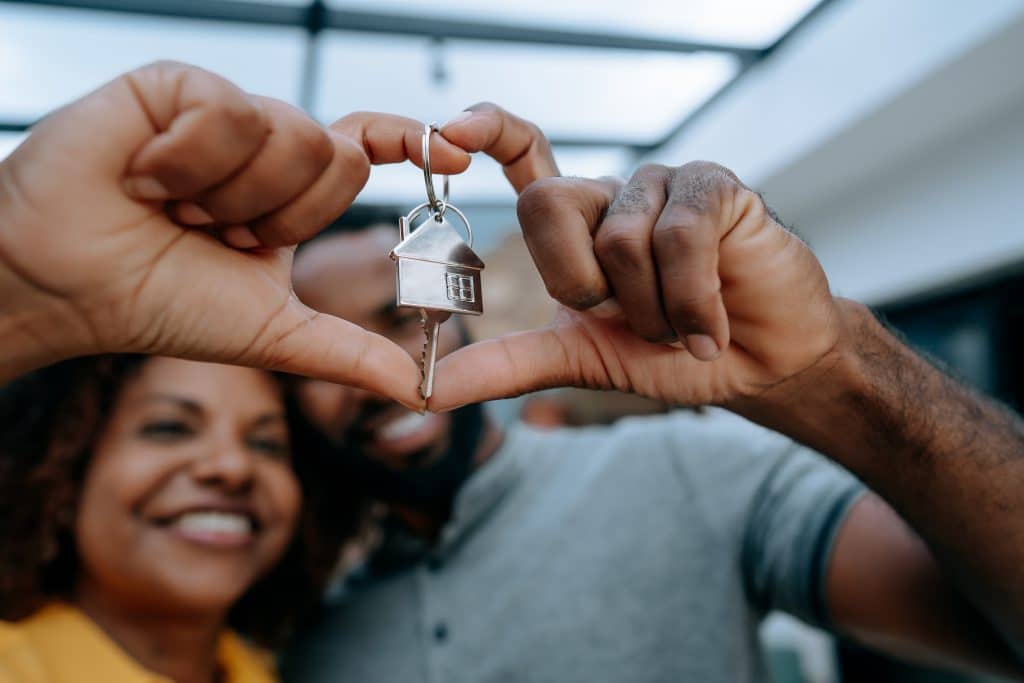